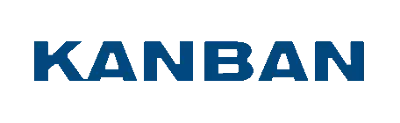
Kanban to metodyka sterowania produkcją, oparta głównie na rzeczywistym zużyciu materiałów oraz na poszczególnych kartach wyrobów a także ich analizie i cyrkulacji. Celem systemu jest przede wszystkim kontrola oraz redukcja kosztów magazynowania materiałów a także jednoczesne zwiększenie dostępności tych materiałów i wyeliminowanie wszelkich przestojów w produkcji związanych z brakiem wymaganych produktów. Podczas redukcji zapasów, zmniejsza się również kapitałowe zaangażowanie ale i zwiększa elastyczność produkcji. Zastosowanie tej metodyki można znaleźć zarówno przy sterowaniu produkcją ale i przy zoptymalizowaniu i zapewnieniu zapasów niezbędnych w produkcji.
Dużą zaletą Kanban jest to, że pracownik w każdej chwili ma dostęp do materiałów, które są mu w danej chwili potrzebne do efektywnej pracy. Natomiast ideę Kanban oddaje tak zwane hasło „siedem razy – żadnych”/ „7 x żadnych”. Ma ona na uwadze:
- żadnych braków
- żadnych kolejek
- żadnych zapasów
- żadnych opóźnień
- żadnych bezczynności
- żadnych przemieszczeń
- żadnych zbędnych operacji technologicznych i kontrolnych.
Metodyka Kanban posiada pewne wiążące zasady, które są niezbędne do poprawnego działania systemu. Do przestrzegania ich zobowiązani powinni być z reguły wszyscy pracownicy będący zaangażowani w produkcję do której wdrożona jest ta metodyka. Wymieniamy takie zasady jak:
- Dostawca nie może produkować na zapas.
- Dostawca musi zapewnić idealną jakość części.
- Odbiorca może zażądać tyle materiału ile potrzeba.
- Odbiorca nie może przedwcześnie wymagać materiału.
- Koordynator Kanban odpowiada głównie za jednolite obciążenia miejsc produkcji.
- Koordynator Kanban odpowiedzialny jest za zapewnienie możliwie jak najniższych liczb kart kanban.
Jest to system dla firm do przekształcania czasami bardzo zawiłych i skomplikowanych kontroli produkcji. Ze względu na wysoki poziom niezawodności i elastyczności dostaw, łatwiej jest zarządzać produkcją za pomocą tej metodyki. Jak podaje wiele źródeł, świetnym przykładem dowodzącym sukces metodyki Kanban jest zdecydowanie firma Toyota. W jej przypadku odnotowane takie wyniki jak:
- 90% redukcji braków
- 60% redukcji wszelkich zapasów
- 30% wzrostu produkcji
- 15% redukcji operatorów i personelu administracyjno-technicznego
- 15% redukcji przestrzeni produkcyjnej.
Natomiast warto dodać, że pewnymi wadami i ograniczeniami metodyki jest na pewno fakt iż Kanban zakłada bezbrakową produkcję, która wymaga całkowitego zaangażowania wszystkich pracowników, co może jednak być niekiedy problemem. Oprócz tego wymaga większej dostępności dostawców, jest mało odporny na spore wahania popytu a koszty transportu zdecydowanie rosną.